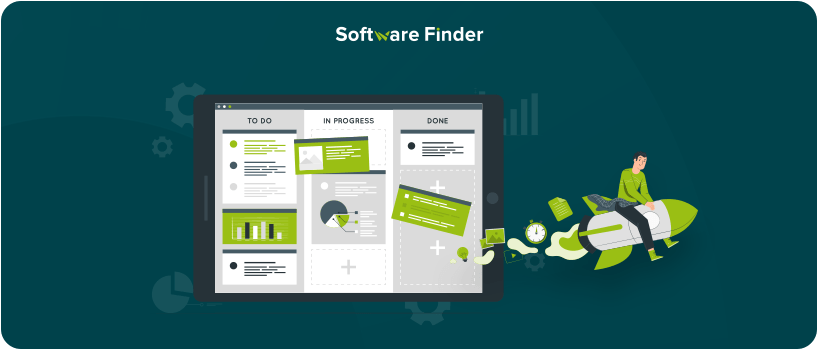
In today’s ever-shifting business environment, the art of project management has become a mixed medium. Organizations must mix and match methodologies to stay on top of things and use amalgamations that best fit their work style. Regardless of the method, incorporating Kanban practices is essential for maintaining an efficient and structured workflow. One of these practices is the process of Kanban inventory management. This blog examines the benefits of employing a Kanban inventory, its key components, practical application, and primary challenges faced during implementation.
Kanban is a scheduling system from the 1940s used to carry out lean and just-in-time (JIT) manufacturing. It is most commonly used in Agile project management to increase communication, transparency, and visibility of the workflow. The main purpose of Kanban, at the time of its inception, was to manage work and inventory as efficiently as possible throughout production.
Kanban inventory management works by aligning products available with their actual consumption. It aims to manage products on a made-to-order basis where only the minimum number of resources are kept at supply points. Inventory levels and production processes are managed through visual signals in the shape of Kanban cards. When inventory runs low, these cards signal when to produce or order more materials. A made-to-order system minimizes waste by ensuring that new materials only come in when they are needed.
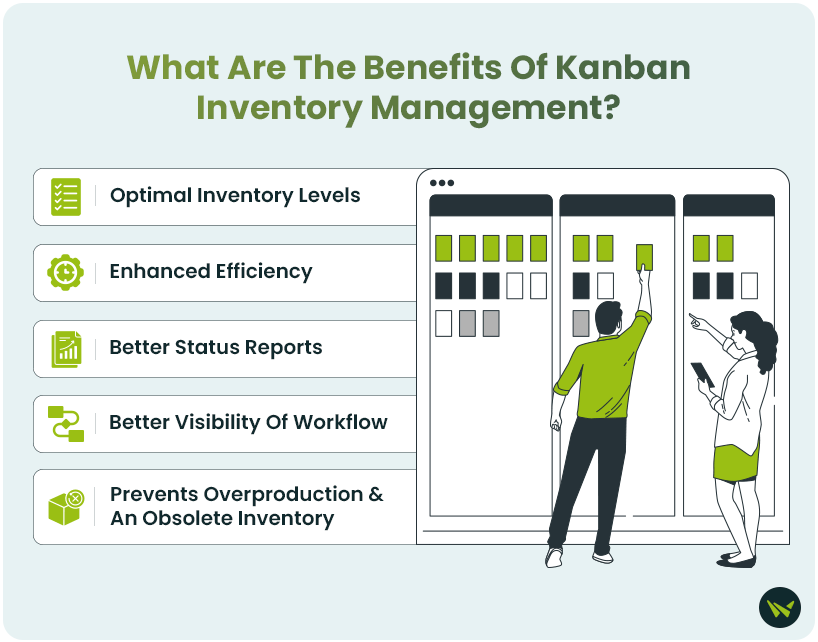
Applying the Kanban method to your inventory management has several benefits, some of which are as follows:
Optimal Inventory Levels
A Kanban ordering system helps businesses accurately track inventory consumption and allows them to restock accordingly. Setting an optimal level and sticking to the limit not only results in a cleaner warehouse that is easier to manage but also prevents overstocking and consequent waste of resources.
Enhanced Efficiency
True to its purpose, kanban inventory prevents inventory buildup by setting limits on supply points. Unnecessary tasks and steps are eliminated, and more focus is given to value-adding activities. Visualizing processes and inventory levels helps quickly identify areas for improvement and prevent potential bottlenecks. The “pull” system ensures that production is done according to demand, reducing lead times and faster production times.
Better Status Reports
With inventory restocks being determined by customer’s demands, a Kanban supply chain system provides managers with better status reports and a more efficient way of keeping up with progress. Customer demands are identified and met quicker, tracking product popularity becomes easier, and the workflow becomes cohesive.
Better Visibility Of Workflow
One of the major benefits of a Kanban inventory system is the increased visibility of the workflow. Cards and boards both represent tasks in a way that allows teams to see the status of work at a glance. Heightened visibility makes it easier to track progress, inventory levels, and identify potential bottlenecks before they become major issues. Better visibility also allows for more transparency and accountability for work.
Prevents Overproduction And An Obsolete Inventory
The Kanban inventory management system aims to prevent increased costs and wasted resources due to unnecessary overproduction. Companies can use Kanban tools to align production schedules with actual demand, resulting in total consumption and, ideally, zero waste. Kanban cards signal when new materials are needed, and businesses avoid wasting time on producing products that are not popular with customers. Only producing what is necessary results in a leaner, more Agile system of operations.
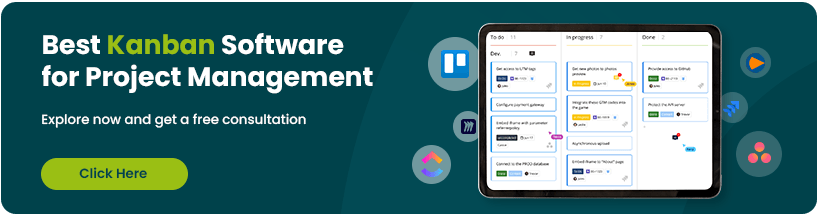
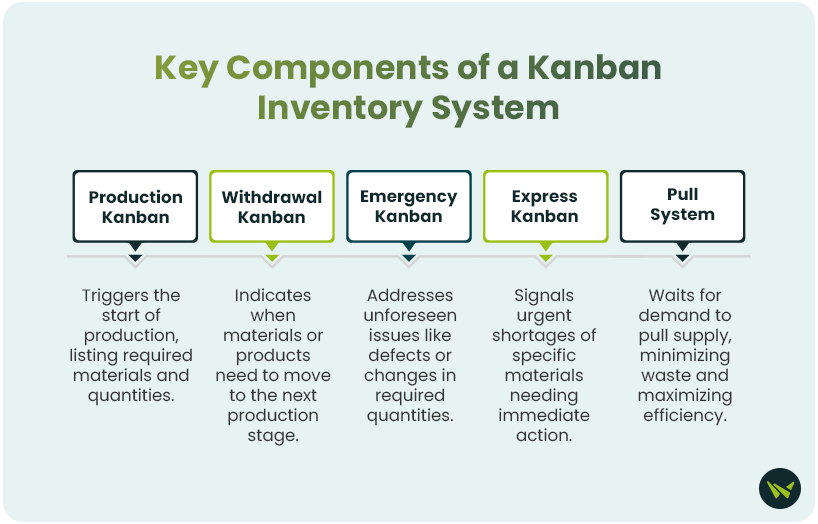
The Kanban system of inventory management functions on cards, boards, and the “pull” system. Kanban cards are distributed on various boards representing different production stages and the availability of materials in the supply chain. Along with the core principles of the Kanban method, the following are common elements of the Kanban inventory system:

Implementing Kanban manufacturing and inventory system helps organizations effectively apply Lean methodology in their production process. The following are the steps you can take to get started:
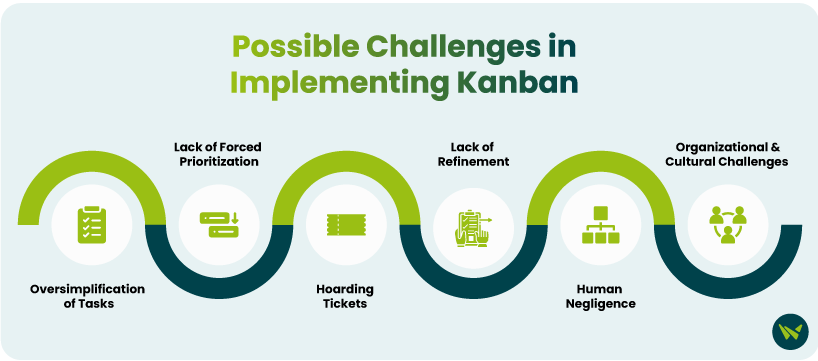
No system is without its due challenges. The following are some common difficulties organizations might face when implementing a Kanban inventory system
1. Oversimplification Of Tasks
If all tasks are represented by simple cards, there is a possibility they start to lack detail. An oversimplification of tasks might lead to lesser clarity. To counteract this, tasks should be broken down into smaller, more manageable steps and those, in turn, should be represented in each Kanban inventory card.
2. Lack Of Forced Prioritization
All Kanban cards appear equal on boards, making it hard to determine priority tasks needing immediate attention. Without a prioritization system intact, tasks may become stagnant and lead to delays.
3. Hoarding Tickets
Limiting WIP is done to prevent the hoarding of tickets. The more active tickets there are at a given time, the harder it is to concentrate on one task. Encourage members to work on tasks they can complete to keep the system moving.
4. Lack Of Refinement
Without regular refinement or grooming of the board, old, irrelevant, or poorly defined tasks can clutter the workflow and hinder productivity. To prevent confusion and errors, regularly review your processes to ensure tasks are aligned with the project's overall goals.
5. Human Negligence
One must always allow room for error on account of human negligence. Team members might mistakenly not adhere to the WIP limits, forget to update cards, and not wait for demand to pull progress forward. Proper training and a culture of accountability can help minimize human errors.
6. Organizational And Cultural Challenges
The successful implementation of a Kanban system requires buy-in from all team members and alignment with the organization's culture. Resistance to change or lack of collaboration can hinder the effectiveness of the system.
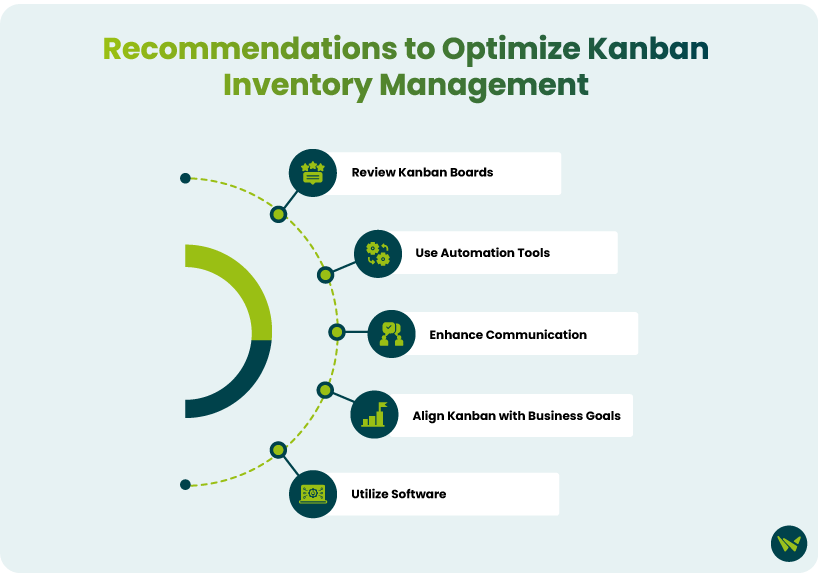
Getting the hang of the Kanban system of inventory management is a practice that requires continuous effort and refined processes. The following are steps you can take to optimize the Kanban manufacturing process:
Kanban inventory management helps teams enhance the overall efficiency of their workflows, optimize inventory levels, and organize tasks. Employing a Kanban supply chain requires vigilance and careful monitoring, but the benefits are worth the effort. Using specialized Kanban software to set up your system helps overcome common challenges and fosters a collaborative environment.